金桔
金币
威望
贡献
回帖0
精华
在线时间 小时
|
这是我最想答的问题,我们在努力。
最后的结果是我们花了三年时间把一个车间缩小到原来的十分之一,产量提高了十倍。补充下,是原年产300吨的产品扩大到3000吨,是连续三步反应。
期间的辛苦远远超出预料,国内硬件的不匹配和过于粗糙,逼得我们搞合成的去设计计量泵,去电焊,去选材料,设备上一套废一套。
说出来只是为了告诉大家这种方式的可行性,让大家更加坚定的走下去。
现在国内化工企业的情况:
1.简单粗暴的工厂迫于环保压力都开始转型或倒闭。
2.废水废气排放控制越来越严格。
3.废水排放量降低,以往清水稀释cod走不通。
4.老生常谈的安全问题
5.其它
针对这些问题我们决定对公司的几家工厂进行改造。
我们需要的是一种基于安全的小型封闭式连续化自控反应体系,并且尽可能的回收废水。
听上去很简单,一套合适的工艺包,几个小反应釜,几台自动进料泵,几根管道,一套自控系统。
继续更
首先老工艺包必须重新开发,所有原料需要满足几个条件:液态,不易结晶,低粘度,同时要控制成本。工艺不便透露,但是我们要做的是挑战经典反应(有固体进料),没有资料参考,没有参考资料,没有资料参考。我们的时间:经典反应,三步反应,一年半,我一个人,经常性加班。结果是:所有固体原料替换,反应比较稳定可靠,废水降低一半,单耗降低20%(大部分废水处理的钱),缺点是:容错性低,没有大设备间歇反应的调整空间大。
工艺出来了就要设计设备,因为不是标准设备,所以大部分都是公司自己设计,最后交给设计院修改,这段时间需要天天和设备部在一起,提供各种参数。结果:一个多月完成。物性书不停翻,拿计算器不停算。
蓝图出来了,最痛苦的设备选型定做开始。结果:大半年设备大体安装完毕。设备调试半年后结果:基本全部换掉,和各个设备厂家留下一屁股纠纷。一年后结果:进料系统和我们想的差距非常大,非常不稳定,需要一直盯着。自动控温系统由于体系太小过于敏感,温差居然上下浮动有30℃。整套系统最满意的就是到处是防爆片。0.25mpa的。
试车:对于实验室来说,工艺就和自己的孩子一样,看在防爆片的份上,我去开车了。不是这段温度超了就是那个进料泵不转了。失败
试车二:设备再次大改,依旧无法稳定可靠运行。
试车三:已经试车一年了,整套设备改的面目全非,自控系统全部撤出,靠活人一直盯着,进料阀门不停调整,到处是我们自己做的小东西。
连续稳定合格出料三天三夜,停车,倒头就睡。
出于对公司的保护,无法详细写出我们如何改进,如何自己制作设备,和众多至关重要的小东西。
虽然很辛苦,国内在这块硬件的制造水平让我们吃尽苦头,工人对新设备的抵触只能自己上,但至少我们做了,这是起点。
有空聊聊我个人对未来化工的想法吧。
在这套设备之前我们还试过一套,去掉反应釜,全是管道,自己改造离心泵,消除它的量程,放在管道直接,用作搅拌和主要反应点,失败了,原因很复杂,国内机械密封太烂,流速过快,换热不够(当然我们已经尽力达到最大换热面积了),但是在某些方便是非常成功的,因为流速快,接触时间短,特别适合会过头的反应,我们的思维模式也在试车中完全颠覆(这类反应实验室都是通过严格控制物料比例和温度来防止过头,然而到最后我们因为换热面积太小,没有控制温度,因为计量泵太差使用略微过量的辅料,单纯通过控制流速得到了比实验室好很多的结果)。思维方式一变,很多不适合工业化的工艺好像有了希望,然后我们就开始自己折腾机封,试过填料密封等等,最后还没办法才有了前文提到的系统。
我还是很心水管道反应器的。
评论区里好多有一样想法的人,甚至还有参加过同一个会议的人,每一条我都认真看了,我很幸运有一个技术狂的老板,给我们足够的自由和资金去尝试,也很感谢设备厂家陪我们折腾,虽然你们并不愿意(看了评论才了解到设备厂家的难处和中国的化工基础设备为什么发现缓慢)
引用几段评论
“我们就是做设备的,最主要还是因为资金的问题,厂商没有多余的资金运用在技术革新上,而人力资源上的节约导致技术人员一个人至少顶着4个活,没有精力在去技术上搞研发,导致各家都是模仿抄袭作假,最终原因还是因为国家的税收太繁多重,利润非常薄”
“原来从事了4年的石化设备,化工泵成套商,下游乙方。。。这个行业的门槛高,各种名单准入机制;这个行业吸金,工程周期长,从产品铸造水平到机加工能力,再到产品质检装配一条线,每一个地方都重要,当然,大部分重工业都这样。正因为如此,这个行业很讨厌的一点就是不肯变动,不论是上游工艺,还是下游设备,都不愿意改动;现在市场上主流工艺和设备,好多还是上个世纪的。。。”
集中回答下几个有意思的问题
1.有没有用到多变量自动控制系统?
答:有,最后都撤了,体系太小,控制点过多,体系小是关键,体系小意味着一切都变得敏感包括液位,温度,压力等变量。而且根据我使用的经验,国内自控阀门多多少少都是会漏液的(等待自控人员解答)体系大的话漏点就漏点,体系小不行。
2.过于小型化,热能这一块有处理方案么?高温高压的作业人员安全以及规范要求在施工图阶段都是需要考虑的问题。
答:热能我们用了两套方案,一是使用大量低沸溶剂,优点是温控稳定,不用依赖自控来控温,缺点是能耗提高,溶剂汽化有压力。二是传统换热器改进,评论区就有人提供这类技术,一定比我们自己专业。
3.感觉主要还是改变设备要变更生产工艺吧,原来的原料指标和加入的比例都会变化。
答:是的,一般人认为原工艺可以直接搬上去用,其实不是的,连续化小型化后物料接触时间和碰撞程度变化,配比是需要变化的。
4.缩小体积,不可避免的带来容错性下降,更别说直接缩到之前的10%。但是自控应该也是可以做到的,能说下问题出在哪里吗?
答:和问题1一样
5.

答:我就是实验室的,三步反应一年半我觉得时间已经足够,控制温度50℃的反应我从冰水温度0℃做到体系沸腾温度110℃,温度破坏性实验全了,体系停留时间也全了,我们甚至定做了一套玻璃连续化小设备运行了三天,物料过量,温度超标,突然停车,体系进水全部现象以及处理方案整理,中式方案其它部分不提,就是工艺方面的应急处理就有十多页,当然我做的并不好,因为这是必不可少的。工人的问题并不是怀疑你的技术,在他们眼里并没有对技术成功的渴望,而是因为改变,让他们上班更加辛苦,他们需要背中控条件,需要摸排新设备新阀门管道,需要接受新的东西,但是工资并没有变化,后来给加了工资还是因为中试太辛苦。你举的例子太赞同了,所以出现了我们自己设计设备的情况,因为非标,一定要化学专业和设备不停的沟通才能设计出能用但是依然很难用的设备。自控阀门更换一定是国内阀门厂的意见,我们并没有这种能力去摸透这些东西,我们只能提供我们的参数,调节阀漏的问题建议你咨询下自控设备从业人选,因为我接触的厂家都是认为有点泄露是正常的,所以我们避开了调节阀。我不知道你是怎么理解走和跑的概念的,有的人沉下心,每天不停的爬,他一定比人早点学会走,每天不停的走,一定比人早点跑,我提到的不多,三年每天我们都在积累。还有,这不是吐槽,如果你是化工企业的,甚至你是我吐槽对象(基础设备行业)的话,大家都有无力感,明明有可以减少污染的工艺,但是成本太高,明明可以更加安全,但是过于复杂。评论区也有设备人员说明明知道是上个世纪设备却无力改变。我写的太少,但是又没办法写出我们是如何修改计量泵,如何让连续化中间的油水分层系统稳定连续,如何让油水在管道中不分层,均匀的按比例流进下一步,如何调节改造连续精馏。你的最后一句我很不赞同,浮躁的有机实验员三年已经走了不下二十个,留下来去做这些事情,扪心自问,都是做好了可能一事无成的准备。最后,逢山开路对于实验室和中试是一定的,我们的技能是尽量在前期减少山和做好遇到山该怎么开路的准备,中试说白了就是熬,不断遇到困难,不断走弯路。
6.
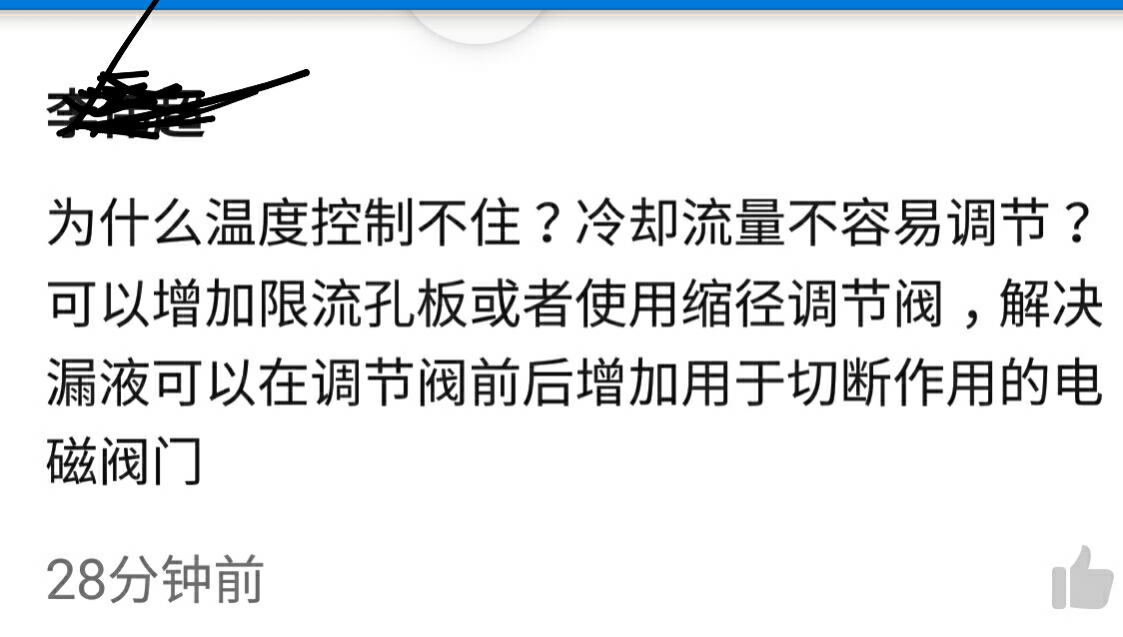
答:温度控制不住主要是换热介质流量不稳定,我们在使用开关的电磁阀时前后都加了阀门,通过缩小阀门来起到缩径的作用(不知道这是否有弊端),运行的还不错,比固定的缩径更加灵活。但是几个小时后电磁阀都烧的差不多了,里面的类似石膏的东西都掉了出来,黑色的油也渗透出来,阀体很烫。可能因为体系调整过于频繁。我们换过好多次,厂家也来换过不同型号,就是一直烧,每烧一次我们都手忙脚乱的,要恢复稳定又要一大段时间,连续化一次不稳定,就是要调整一大段时间,最后就都撤了。
继续留着,有空慢慢说。
再说一下,这真是个好问题啊!是未来化工的一条很不错的路。
我们也考察了很多企业,康宁的微通道反应器,某公司的回路反应器等,最后还是选择自己做。
各位同行并且有同样想法的甚至是在和我们做同样事情的人,非常抱歉,我们还没有对外交流的打算,希望我们能一起平行向前,前面一定会有个交点。 |
|